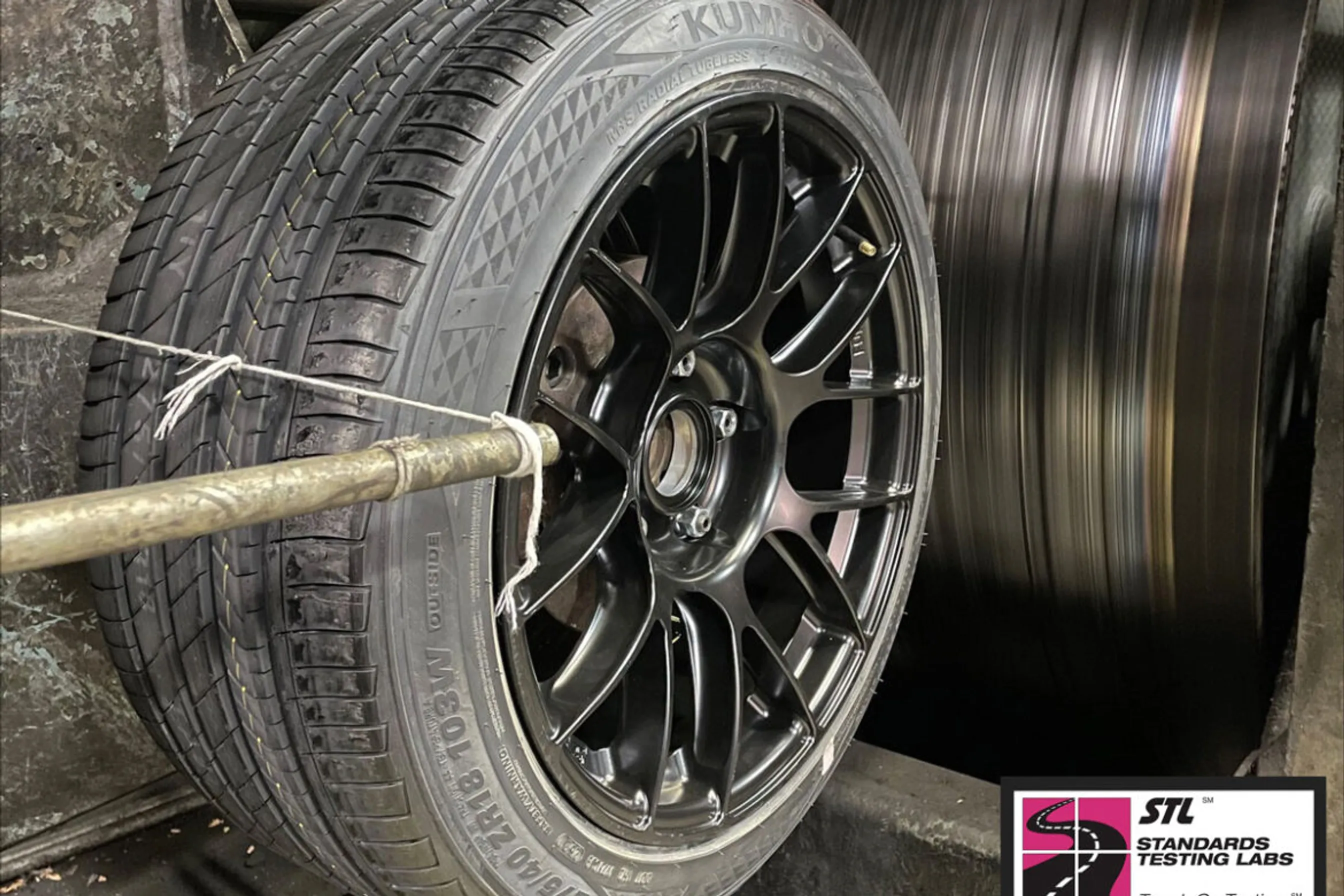
Testing to a Higher Standard
Article | 11/08/2021 by Apex Wheels
Updated on 08/06/2024
The wheel industry in the United States is unregulated. There are no testing requirements, no inspections, and no organizations policing false claims. That has left the door open for many wheel brands to take advantage. Safety testing in this industry can vary widely, from no testing at all, to independent testing conducted by an unbiased 3rd party with verifiable results.
Unlike the US, countries like Japan, Germany and Austria have required testing standards and independent or governmental agencies to conduct mandatory, destructive tests. We wish the US had similar regulations, so consumers wouldn’t have to blindly trust manufacturers, and we wouldn’t have to compete in a market where the claims of brands that either don’t test properly or misrepresent their certifications, are perceived as being equal to our extensive – and expensive – safety testing and certifications.
These issues are why we believe consumers need to demand that wheel companies provide proof of testing conducted by an independent agency without bias. From the day we first started selling wheels, APEX has been following international standards voluntarily, and sending our wheels to the Vehicle Inspection Association (VIA) in Japan for independent testing and certification. With the launch of the Sprint Line, we wanted to highlight the enhanced capabilities of these new forged wheels. Some of the improvements were so significant that getting a traditional VIA certificate would do our wheels a disservice, so we began sending our forged wheels to Standards Testing Labs (STL) in Ohio to test them to even higher standards, and have since moved that testing over to Independent Test Services (ITS) in Canton, Michigan because of their faster turnaround times.
STL is the largest, independent, dynamic-testing facility in the world, but they were acquired by a larger organization and it became harder to work with them. We originally chose to work with them because the VIA will only perform a pass-fail test. We appreciate that the VIA is an exceptionally detail-oriented agency, with multiple levels of audits in place to ensure that tests are conducted exactly to JWL specifications. While this ensures you can have maximum confidence in a legitimate VIA report, tests are conducted to 100% of JWL specified loads and no higher. STL was willing to independently validate the result of any well defined test and run it beyond a mere pass, all the way to failure. We asked STL to conduct more rigorous tests, with higher loads and longer durations than those required by the JWL standard. ITS performs the same tests and we’re excited to do experiments with the more advanced equipment ITS has, such as their biaxial fatigue testing machines that can simulate driving on track and not just standard loads.
Every prominent testing standard including JWL consists of three different tests; cornering, impact, and radial. The cornering test puts a bending load on the wheel to simulate hard cornering. This test is very meaningful for road racing applications where high-grip tires and high-G turns can crack a wheel’s spoke. The Impact test strikes a wheel that has a tire mounted to ensure the assembly can still hold air after hitting something like a curb. The radial test is also done with a tire mounted, and it applies a downward load far in excess of even the heaviest of cars, or ones with a lot of aerodynamic downforce.
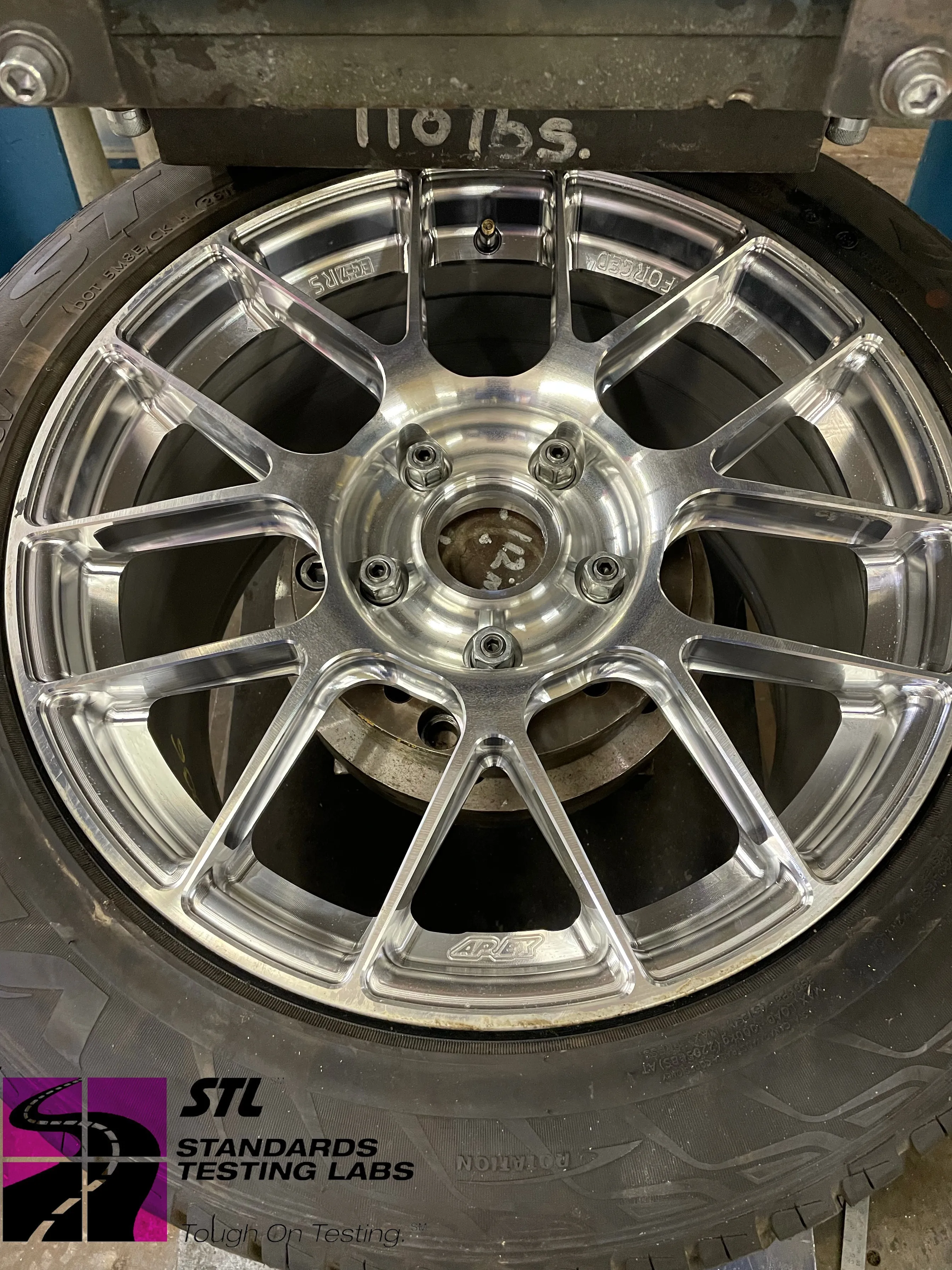
JWL standards set specific load requirements for wheels, which vary by bolt pattern and diameter. A wheel could be engineered to have a higher load rating than the requirement but the VIA will only conduct the test to the JWL standard. For example, Corvette applications call for a load rating of 1334 lbs. Our lightweight Sprint Line wheels for Corvette have a load rating of 1600 lbs even though others on the market may only choose to follow the required standard. To verify our higher load rating, the labs we work with have to increase the loads of all 3 tests; a higher load is applied during cornering and radial testing, and a heavier weight is dropped for the impact test. Both labs followed the JWL formula, they just increased the load variables.
Additionally, we extend the duration of the tests by either running the wheels to failure or stopping at a reasonable point. For example: The duration for the JWL cornering test is 100,000 cycles. The test of our VS-5RS wheel was conducted at a higher load until it failed at 362,709 cycles – 362% of the JWL requirement. The JWL radial test calls for 500,000 cycles. We’ve run experiments internally out to 2,000,000 cycles, but running a test that lasts that long at an independent lab is very expensive, so at STL we’ve been cutting off the test after 1,000,000 cycles or 200% of the JWL requirement. For comparison, there’s another testing standard called SAE J2530 which calls for 1,100,000 cycles for the radial test. That sounds impressive, but the SAE test is run with a lower load, which results in very similar fatigue to the JWL test even though the SAE duration is twice as long.
The wheels tested by these labs are the highest-stress specification that can be made from our motorsport dies, in each diameter, and for each design. For the 18” wheels, that specification ended up being 18×11” ET88. We don’t expect to ever create a wheel with such a high offset in that particular width, but the combination of very flat spokes and a wide barrel was the highest-stress fitment based on analysis of every width and offset combination. Internally we conduct additional tests to simulate other outlier fitments, as well as extensive, repetitive testing of a single specification so we can create SN curves and determine design limits to better improve our computer modeling. For example, we machined about 20 units of the exact same wheel and ran all of them through the same test with only slight changes in the load applied. That experiment helped us optimize our wheels so they could be as light as they are, while being as strong as they are. Although we test far more wheels internally, we continue to rely on VIA, and now also ITS testing to essentially act as an audit and confirmation of our work, and for consumers they act as a check against possible miscalculations in engineering.
Below you can find copies of the STL and ITS test reports for each design and diameter of our forged wheels. We’re working on creating a new page on our site to better organize data like this.
VS-5RS
20" - STL Cornering Test Report
SM-10RS
EC-7RS
VS-5RE
SM-10RE
ML-10RT
Tags

If you like cheap gear you will hate this newsletter.