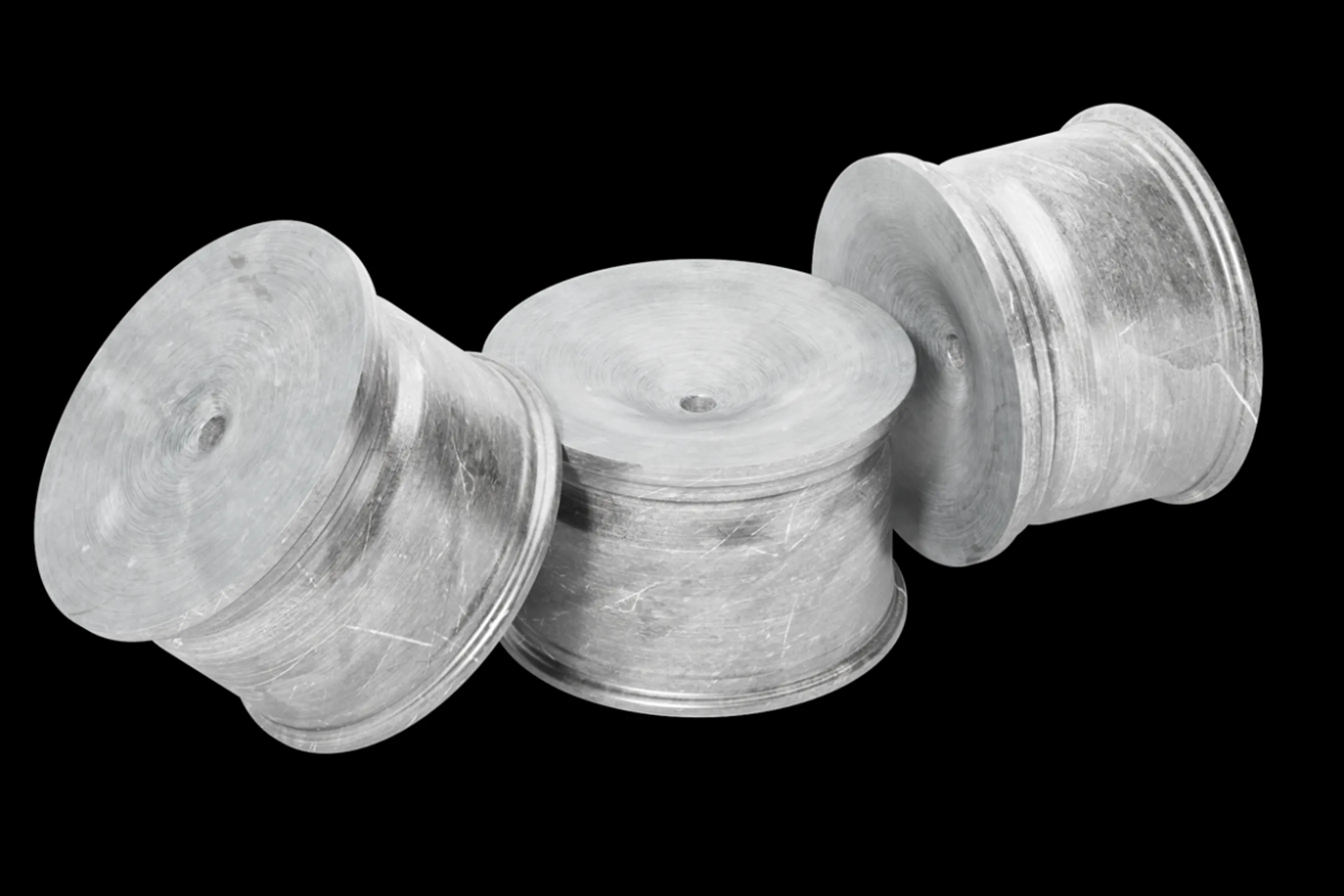
All Wheel Blanks Are Not Created Equal
Article | 11/05/2021 by Brandon Kimbell
Updated on 08/27/2024
For our forged wheels to include the key motorsport features we wanted, we had to design new forging dies from scratch. It’s been a multi-year project, but it was the only way to ensure we could clear more brakes, create lighter and stiffer designs, and add a lot more inner lip strength.
Motorsports are Niche
The majority of forged wheels sold around the world are not used for racing or motorsports, they’re just used on the street. It makes financial sense for a forging supplier to optimise their blanks for the production of simpler street wheels. Why incorporate expensive features into a die and drive up the cost of all their wheels if only a small percentage will be used in demanding applications? Because featureless blanks intended for basic street-wheels cost less, there’s a big trend for brands to create wheels using them and design wheels that scream motorsport with their styling, yet be compromised on key features.
All manufacturers are limited by what they can machine out of the raw forgings available to them, which are often purchased from and designed by a 3rd party supplier. Because APEX is focused on motorsports, we had to design new forging dies in order to create the wheels we wanted. We took years to roll out our forged wheel program as there were huge hurdles and costs to creating new dies. We did not want to compromise our designs by using existing blanks. We could have made wheels that are technically forged, but they wouldn’t have lived up to our standards and values. In this article we’ll cover the biggest difference between what APEX can produce with our Motorsport blanks vs. the limitations of what we call Street blanks.
Strength and Stiffness:
To make wheels as light as possible you have to find more efficient ways to make them strong. One of the best ways to make a wheel extra stiff is to make the spoke narrow yet deep. When you compare our original EC-7R to our EC-7RS you can see that we’ve elongated the “I” beam spoke effect by making the spokes significantly deeper. Doing so allowed them to shed weight while at the same time increasing stiffness.
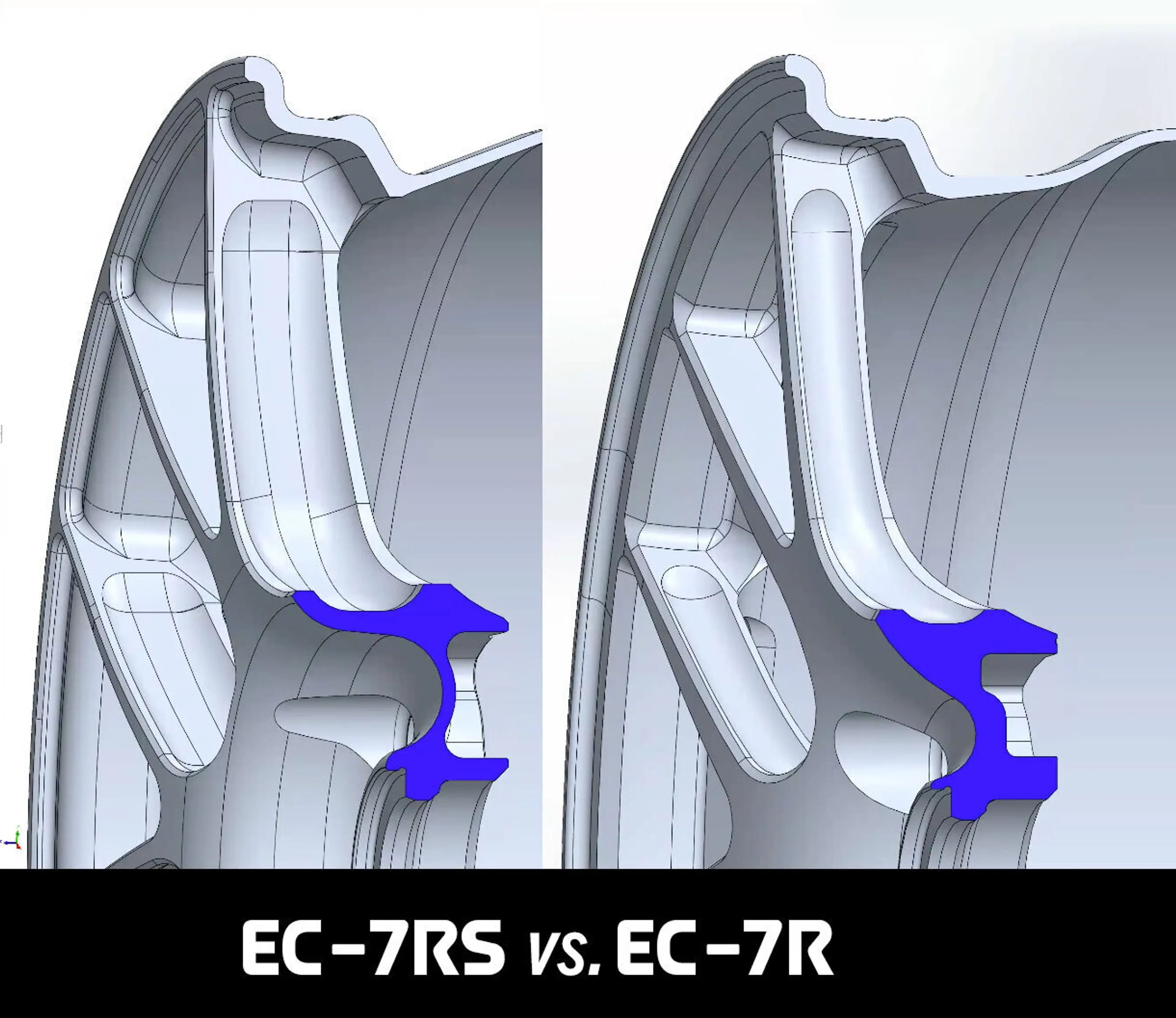
This can’t be done with a Street Blank that has limited material in the face. For cost reduction, most forging blanks are optimized to be shallow to reduce the amount of aluminum in the raw forging. A typical 18” blank may weigh 80-90 pounds before machining, but ours weigh 120 pounds, allowing us to fabricate to have deep spokes regardless of the spoke’s curvature.
Barrel Clearance:
Our motorsport blanks feature maximum-clearance, zero-degree-draft barrels. This allows us to clear more brake calipers, ensuring drivers aren’t forced to buy the next size up in diameter which is a performance killer, as well as a wallet killer.
Creating a high-clearance barrel is easier said than done and costs a lot to do right. Forged wheels have their barrels formed by high pressure rollers that stretch the wheel’s barrel out over a drum or mandrel. In order to be removable from the machine the barrel needs to have a slightly tapered angle to it, otherwise it will get stuck. The problem with adding a tapered design to a barrel is the barrel gets tighter the closer you get to the face of the wheel, which compromises caliper clearance. For a lot of applications, that doesn’t matter and it’s cheaper to just use a tapered barrel, but if those extra few millimeters make the difference between being able to run 18” wheels instead of 19” wheels, then those clearances matter a lot. To get rid of the taper and increase barrel clearance, we roll out a much thicker barrel initially, then we machine the tapered section off, allowing us to create a zero-degree draft barrel, which is the absolute maximum clearance possible in a barrel.
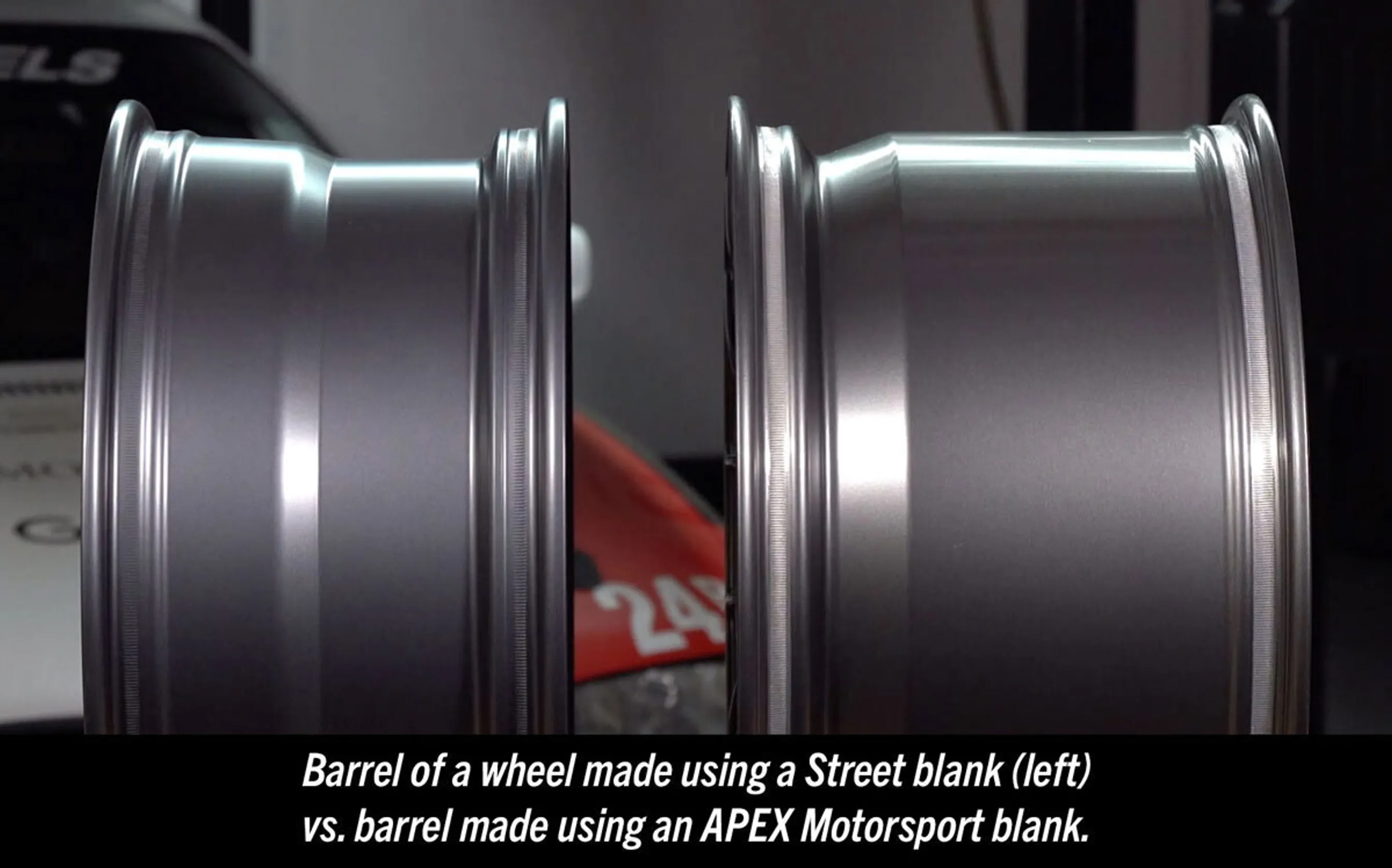
One of the easiest ways to spot a wheel that’s made using a Street Blank is to look at the barrel shape. If it has a heavy taper or a drop-well that’s unusually wide, then it was probably designed by someone who was not prioritizing brake clearance, but by someone prioritizing cost reduction. It’s surprising how many of those wheels are being advertised as engineered for big brake clearance when they simply aren’t.
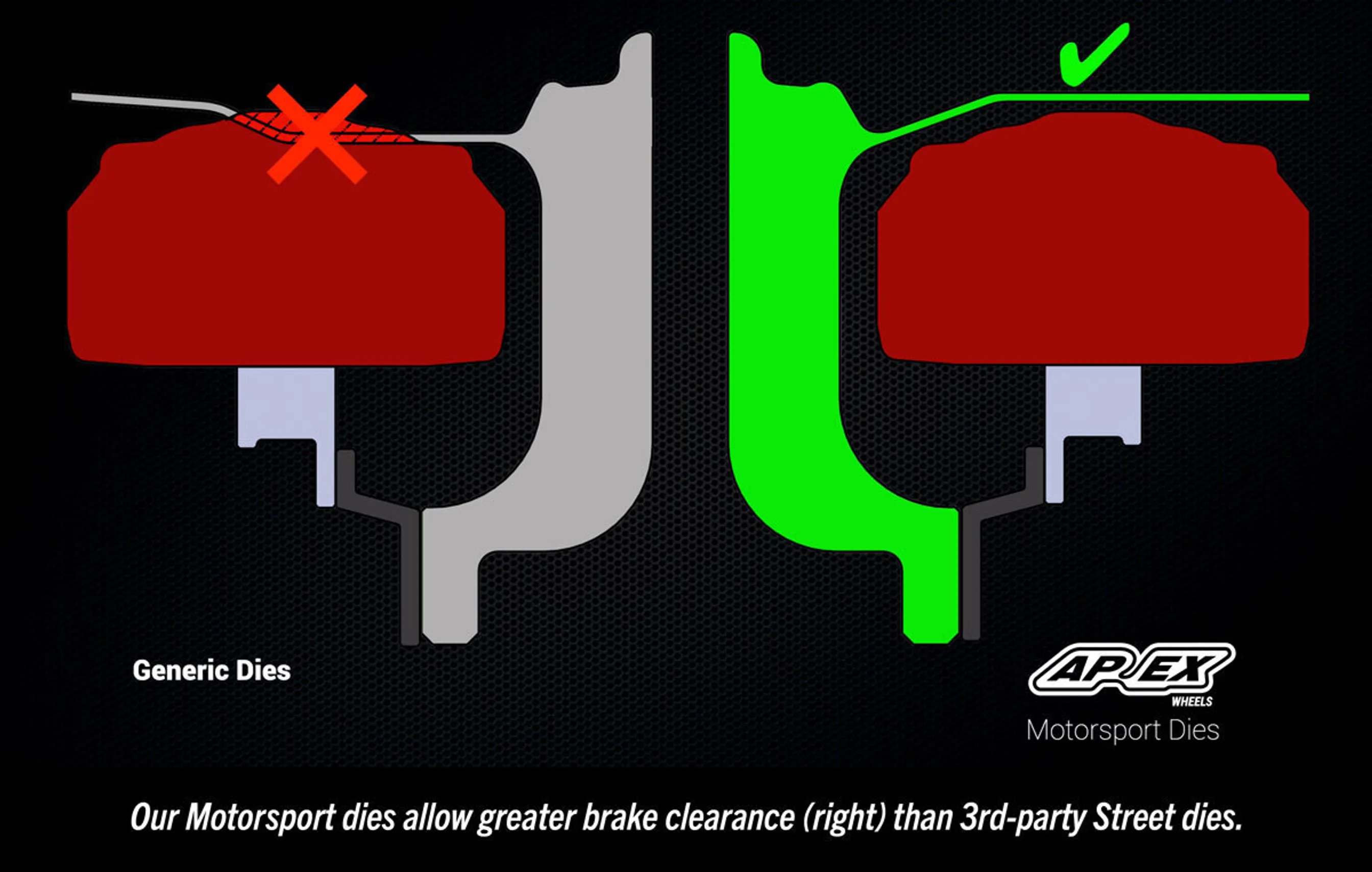
Inner Lip:
Our Motorsport blanks feature extra material in the inner lip section allowing us to make significantly stronger lips for motorsport and heavy duty endurance applications.
You can’t just add material anywhere on the lip to meaningfully increase strength, Extensive testing found that we had to add material in a non typical area to get the most weight-optimal strength increase. To add thickness where we needed it, we were forced to change how the entire barrel is formed during production. To change the barrel, we had to change the die itself. If we were forced to produce wheels using 3rd party blanks, then our inner lip would be significantly weaker as those blanks simply have too little material in them. Those wheels may have been cheaper but they’d also be weaker. Inner lip strength is the wrong place to take a shortcut in order to cut costs.
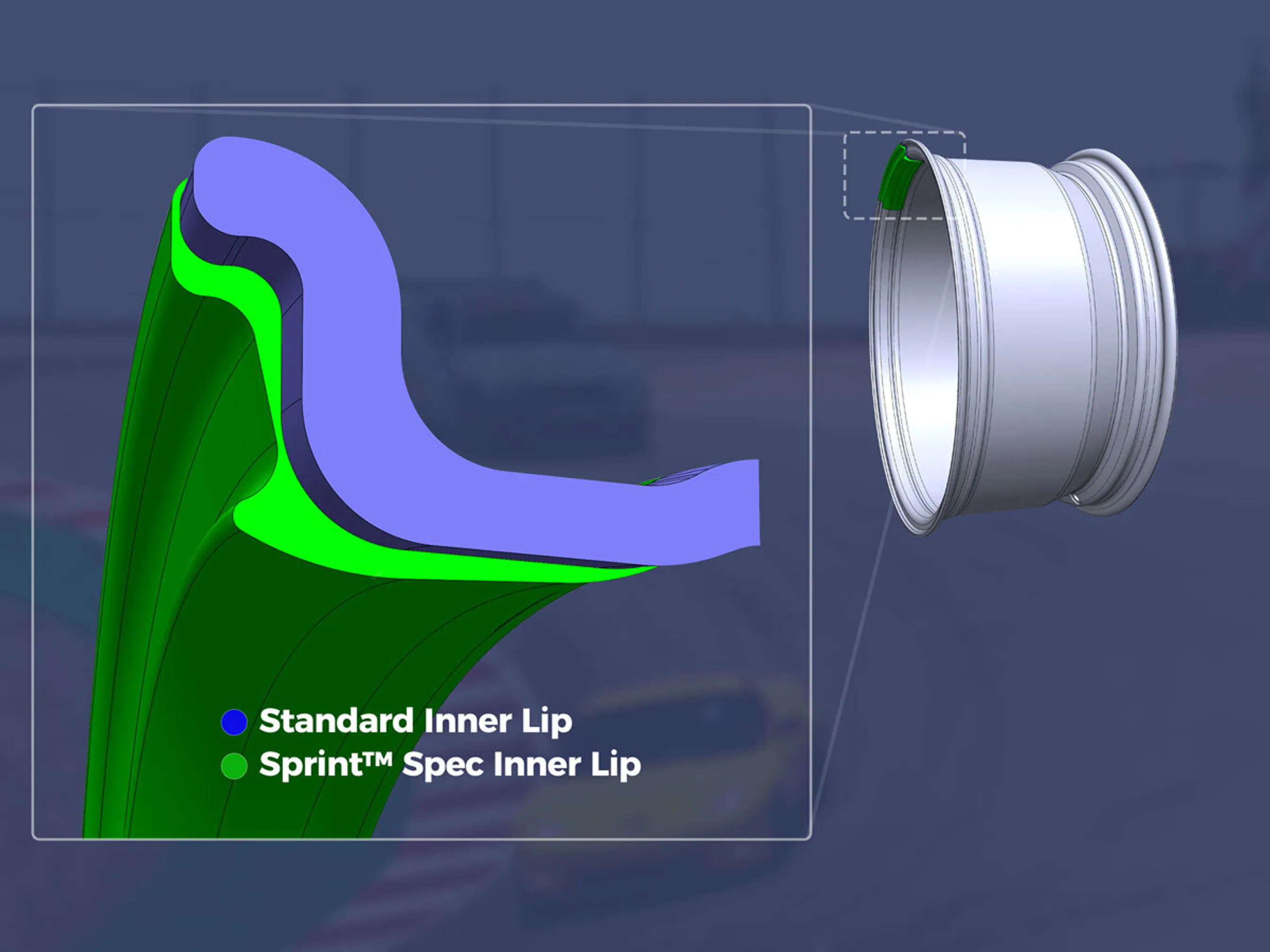
Spoke Curvature and Concavity:
Our motorsport blanks feature an extra thick face area. This allows us to make pretty much every spoke curvature profile we would ever need to clear calipers at all sorts of offsets. We can make spoke profiles that are flat, medium, deep, and everything in between, which allows us to optimize strength and weight. There are plenty of forged street wheels with deep concavity, but when they come from a forging blank that lacks the type of barrel and inner lip that’s needed for motorsports, then they’re simply a fashion wheel for the street.
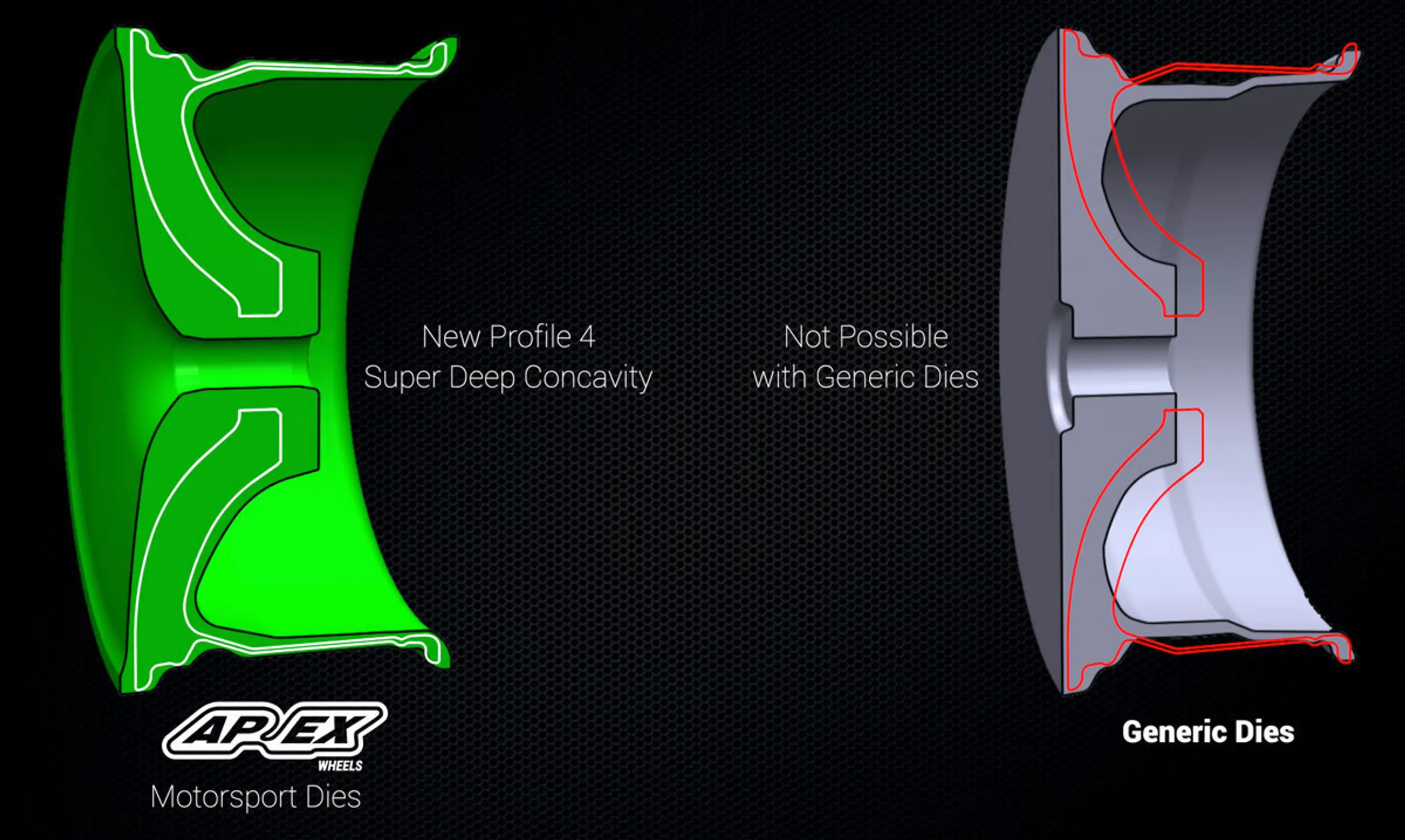
Street blanks often prioritize cost savings, and one of the best ways to save money is to limit the amount of aluminum available in the face of a wheel. That restricts the curvature of a spoke to a narrower range, often leading to flat designs being used on wide, low-offset wheels that would have greatly benefited from a more concave spoke. The problem with flat(ter) spokes in those applications is that they experience greater stress without additional reinforcement. That extra reinforcement to the spokes leads to heavier wheels.
Big Potential – Big Value:
These new dies enabled us to make our new lightweight sprint line, but they’ll also allow us to create other wheel lines such as heavy duty, high load rating endurance wheels for the most demanding of motorsport applications. When you factor in every feature we ensure is in our new forged wheels, then you can see why they are such an incredible value. Not all forged wheels are alike, and you can’t compare the bargain, motorsport-looking wheels made from street blanks with motorsport styling to a feature- packed, motorsport wheels, engineered from the ground up. If we wanted to make a quick buck, we would have been selling a wide range of forged wheels long ago. We’re motorsport enthusiasts who are passionate about what we create and put our name on. These motorsport dies ensure we can be proud of everything we produce from them.
Tags
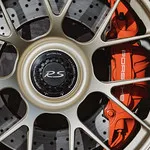
Brandon is a Porsche Fitment Expert at APEX Wheels. Prior to joining APEX in 2022, he worked as Office Manager for a Porsche & Ferrari service and race shop, guiding customers in all areas – suspension, power, aesthetics, you-name-it. His first foray into racing came In college when he was asked to assist at a PCA club race. Says Brandon, “I figured if I am already making the drive, I might as well enter the HPDE happening at the same time.” He hasn't stopped since. Among the various cars he has owned and/or tracked are a ‘74 Corvette Convertible, ’74 Firebird Formula 400, ‘17 GTI, ‘07 Cayman S, and his current ride, a ‘12 Cayman R (BGB X51 pack 3.8L) with staggered APEX EC-7RS 18x9”ET46 & 18x10” ET36 in Motorsport Gold. Fun Fact: Brandon is a big fan of SIM racing, which he uses to learn about a new track he’s going to or get a refresher on a familiar track, as well as improve his racecraft.Have questions about wheels for your Porsche? Use our contact form and ask for Brandon.
If you like cheap gear you will hate this newsletter.