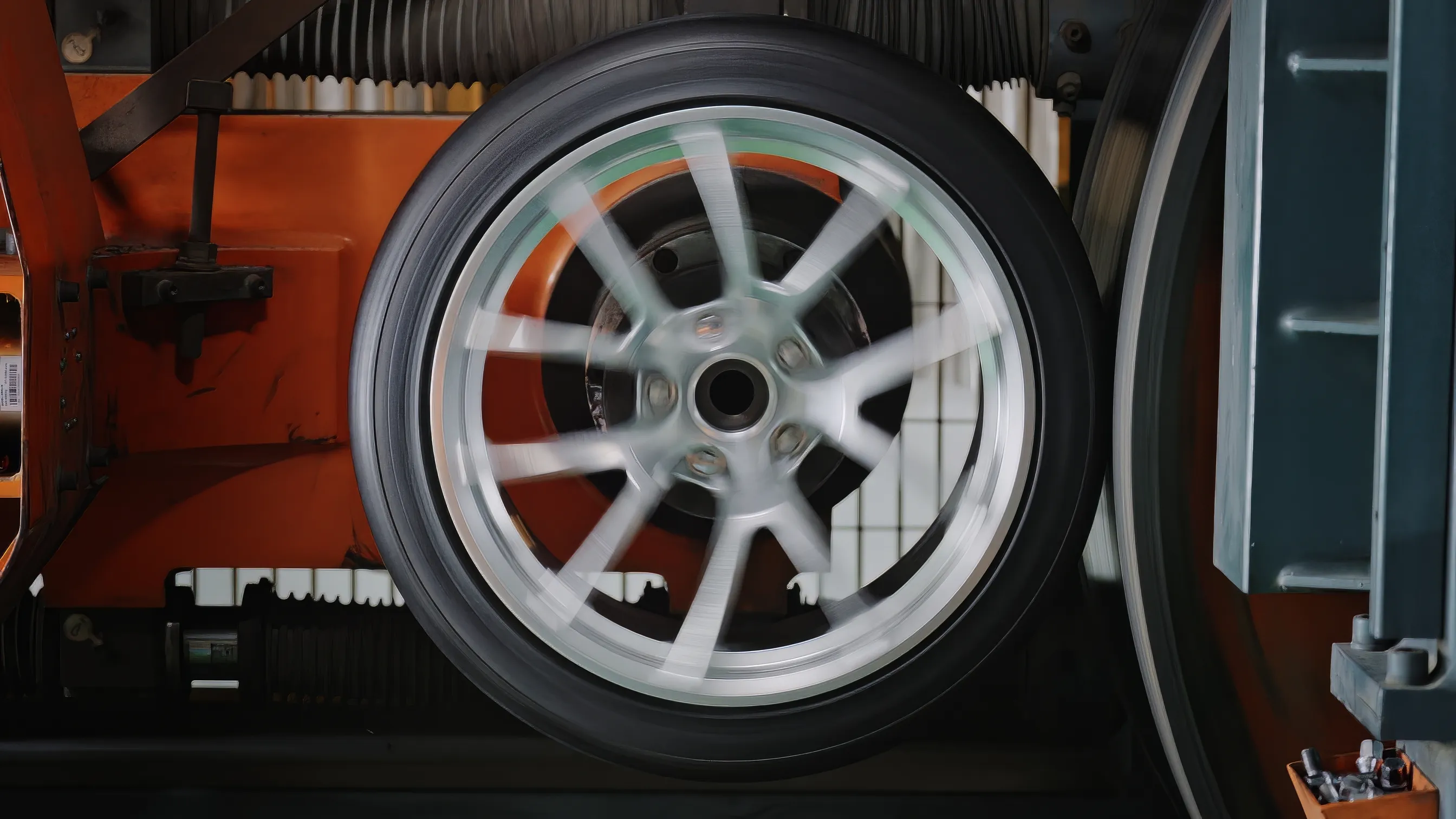
Wheel Industry Myth: All wheel manufacturers conduct real world tests of their designs
Article | 03/19/2024 by Ryan March
Updated on 08/27/2024
If you thought all wheel manufacturers conducted real-world destructive tests of their wheel designs, then you were wrong. Many wheel designs sold today are totally untested or are improperly tested in laboratory tests, leaving many to be only computer simulated. Surprisingly a lot of the most expensive wheels fall into the untested category. Do you know how the wheels you wanted to buy are validated?
Despite their low cost, cast and flow formed wheels are more commonly tested in laboratories using bending, impact, and radial load machines. The high volume of production makes the cost of testing reasonable to amortize across large batches of production. Custom forged wheel manufacturers on the other hand like to avoid real world testing because production volumes are way, way lower, and they typically offer a wide range of designs. If each one of those designs was tested fully then it would gobble up their profit or force them to charge even more. Many new cheap brands that pop-up also limit or skip testing as a way to be faster to market and cost competitive even when they only offer a few designs.
Imagine if a wheel manufacturer that was making you a custom set of wheels in a special size and design just for you had to also make an extra set to destructively test those wheels. Now imagine they made a mistake in the design and it failed, so they had to revise the design and make another set to test again, and do this over and over until it passed. It would make custom prices double or triple if not more. So when you’re buying wheels from a company that’s chosen to rely on computer simulations (FEA) then you’re getting only a certain amount of engineering effort. Safety validation and testing is cut or limited to a level that remains profitable at that scale.
We’ve designed wheels that have passed our R&D simulations but failed real world experimental testing, which is why we keep refining our models by calibrating our FEA off those tests. Our goal is to get our software simulations to the very edge of predicting real world results, so that adding safety margin is done with intention and not out of blind necessity. We’ve seen a huge disparity between manufacturers on how well those FEA models represent real world tests, and even the best models aren’t perfect. An engineer at one company might use a completely different simulation model from the engineer at another company. We’ve seen shockingly primitive models that stand no chance of representing real world stresses. Fixtures are modeled wrong, oversized meshes are used, loads aren’t modeled well, or analyses only simulate a few load cases. Even complex models don’t account for everything and can result in false positives and wheels that fail real world tests. Bad models are leading to wheels getting to the market that would not have been approved for production by manufacturers that do tests to confirm their designs. If you don’t test but you want to be safe then you have to be overly conservative with a design and limit optimization leading to non optimal designs. If you don’t test you can’t be confident what will and won’t work.
Since no testing is required in the USA, a company is allowed to crank out any design in any spec and quantity. It's why the custom wheel market flourishes here in the United States while prominent brands from more regulated countries don't have custom wheel programs. Some wheel companies will be transparent and admit to relying on simulations only, but there are a lot that are not transparent, leading to misunderstandings or misinterpretations that can benefit their sales. Although it’s not legally required here in the US, do you really want to give up testing for a high performance application? Would you buy a helmet or racing harness that was only computer modeled and never physically tested? They have those on ebay right now on sale.
What can create additional confusion is manufacturers that conduct real world tests but they are done “in house”, meaning self conducted without independent oversight. Read our other article about how easily these tests can be done wrong or cheated, leading to false conclusions or a false feeling of safety.
At Apex, we will forever be chasing improvements to our computer models. Forever trying to get closer and closer to accurately predicting what would happen in the real world. Improving our models requires a lot of real world testing to calibrate, so we’ll never stop our real world testing. We believe that independently conducted laboratory testing by a 3rd party is the right way to keep products in check that are intended for extreme use in motorsport applications, or even just taking your family to soccer practice.
Tags

If you like cheap gear you will hate this newsletter.